فورج یا آهنگری شامل ضربه و فشرده سازی فلز بوسیله ی ابزای مانند پتک یا چکش است. به عملیات فورج فولاد، چکش کاری نیز گفته می شود. انواع فلزهای سنگین و سخت قبل از عملیات فورج به عملیات حرارتی نیاز دارند؛ ولی فلزهای نرم تر مانند برنج، مس و آلومینیوم را می توان بدون نیاز به عملیات حرارتی و به صورت سرد آهنگری انجام داد. بدون در نظر گرفتن گرم یا سرد بودن روش این فرآیند فورجینگ شامل استفاده از یک نیروی زیاد با استفاده از قالب یا وزنه سنگین است.
چکش کاری
فورج و آهنگری یکی از روشهای شکل دهی فولاد است. این فرآیند از گذشته مورد استفاده بوده و اکنون نیز یکی از روشهای ساخت ابزار آلات و قطعات فولادی می باشد. قاطعانه میتوان گفت که آهنگری یا چکشکاری قدیمیترین و کهن ترین روش ساخت و شکل دهی فلزها از جمله فولاد و آهن می باشد.
اگر فولاد تا دمای بسیار بالایی گرم شود، انعطاف پذیری و چکش خواری آن بهبود مییابد. تحت این شرایط میتوان آن را با ضربه زدن و یا اعمال فشار، تغییر شکل و فرم داد. انجام فورجینگ به روش گرم به یک کوره برای بالا بردن دمای فولاد نیاز خواهد داشت. در نتیجه ی این افزایش دما در عملیات آهنگری، نیروی لازم برای تغییر شکل فولاد کاهش می یابد. از این رو در بیشتر کارخانههای تولید فولاد، فورجینگ در دمای بالا انجام میشود. اما میتوان برخی از موارد فورج را به صورت سرد و در دمای پایین انجام داد.
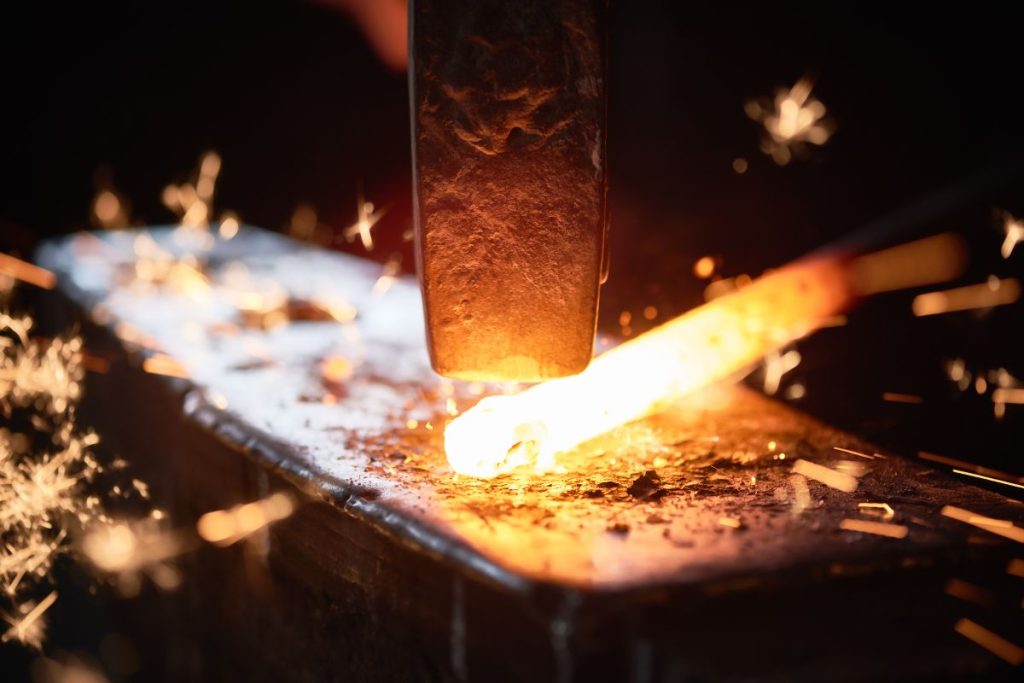
انواع روشهای فورج فولاد
روش های فورج تقریباً ضایعات بسیار کمی دارند و نسبتاً بدون ضایعات می باشند. این روش ها می توانند ابعاد و هندسه قطعه نهایی مد نظر را در مدت زمان کوتاهی در یک یا چند مرحله فورج یا چکش ایجاد کنند. فرآیند فورج، عمل ضربه زدن باعث شکلدهی فلز بدون آسیب به جریان ذرات میباشد. به همین علت فلز استحکام خود را حفظ میکند. در حال حاضر این فرایند، طبق درجه حرارت به این صورت طبقهبندی میشود؛
- آهنگری سرد
- آهنگری گرم
- آهنگری داغ
-
فورج یا آهنگری سرد فولاد
فرآیند فورج سرد فولاد (Cold Forging) در دمای کاری حدوداً ۱۵۰ درجه سلسیوس است. در این روش به نیروی بسیار زیادی برای تغییر شکل فولاد نیاز است. همانطور که میدانید در این دما محیط فولاد دارای استحکام بسیار زیادی می باشد پس برای تغییر شکل آن نیروی بسیاری زیادی نیاز داریم. این روش به دلیل پایین بودن دمای انجام عملیات بر روی سطح فلز، اکسید کمتری نسبت به فورج داغ ایجاد میکند و همچنین قطعه حاصل کیفیت سطحی بالاتری خواهد داشت.
-
فورج یا آهنگری گرم فولاد
فرآیند فورج گرم فولاد (Warm Forging) در دمای کاری حدوداً ۷۵۰ تا ۹۵۰ درجه سلسیوس است. در این محدوده دمایی شکل پذیری در حد مطلوب و خوبی می باشد ولی نسبت به آهنگری داغ نیاز به نیروی بیشتری به منظور تغییر شکل فولاد خواهیم داشت. در این روش فلز تا دمایی پایینتر از دمای تبلور مجدد، حرارت خواهد دید.
-
فورج یا آهنگری داغ فولاد
فرآیند فورج داغ فولاد (Hot Forging)، در دمای کاری حدوداً ۹۵۰ تا ۱۲۵۰ درجه سلسیوس می باشد. دلیل داغ کردن فلز تا این حد، عبور از دمای تبلور مجدد آن است. انجام فرآیند فورج در این دما به نیرو و فشار بسیار کمتری نیاز دارد و میشود با صرف انرژی کمتر شکل پذیری خوبی را شاهد بود.
عملیات آنیل کاری
به منظور زیاد کردن انعطاف پذیری و کاهش سختی فولاد، بر روی آن، آنیل کاری انجام خواهد شد که قسمت مهمی از فرآیند فورجینگ می باشد. در نتیجه آنیل کاری (Annealing) کارپذیری فولاد افزایش می یابد. همچنین فرآیند آنیلینگ، فولاد تا دمایی بالاتر از دمای تبلور گرم شده و برای مدت زمانی در آن دما باقی خواهد ماند. سرعت سرد کردن آن پس از آنیلینگ به نوع فلز و ویژگی های آن بستگی دارد.
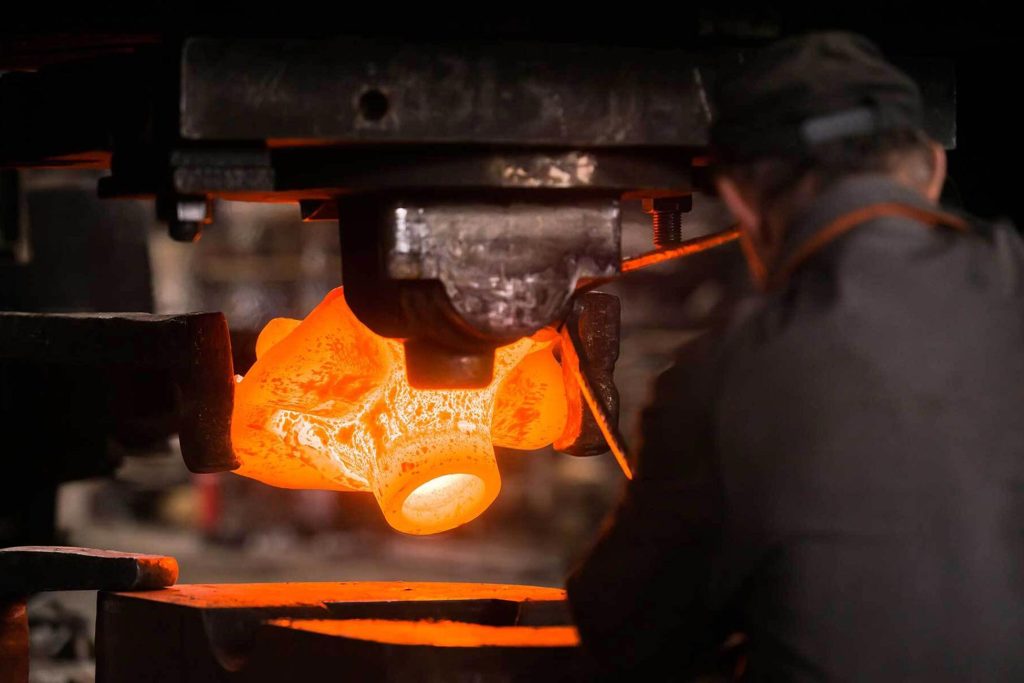
برای مطالعه ی این مقاله بر روی متن فوق کلیک کنید!
به منظور فورج فولاد، از نظر هندسه قطعه و نوع آلیاژ، ۳روش برای انجام این فرآیند به شرح زیر هستند؛
- فورج دقیق
- فورج قالب باز
- فورج قالب بسته
فورج دقیق
در فرآیند فورج دقیق، میبایست ابعاد قطعه دقیق مشخص شود تا بدون حضور مادهای دیگر قالب را پر کند. اغلب آهنگریهای سرد در دسته فورج دقیق قرار می گیرند و در بعضی موارد روش گرم نیز روش دقیق می توان باشد. در این روش محصول نهایی دقیقاً و یا شبیه همان شکل مورد نظر خواهد بود. از این رو قطعه خروجی نیازی به ماشین کاری ندارد و در صورت نیاز، بسیار کم است.
فورج قالب باز
در فرآیند فورج قالب باز، با استفاده از یک چکش یا هر عاملی که قادر باشد نیروی زیادی بر قطعه اعمال کند، ضربات زیادی به فلز وارد میشود تا آن را تغییر شکل دهد. محصور نبودن فلز یا قطعه در میان قالب و دیوارههای آن موجب حرکات آزاد آن در راستای طولی و عرضی خواهد شد. قطعات بزرگی که امکان تولید آن به روش قالب بسته وجود نداشته باشد را به این روش تولید میکنند. قالبهای این نوع فورج اکثراً مسطح است و برای تولیدات خاص، قالبهایی با سطوح ویژه استفاده می شود.
فورج قالب بسته
در این فرآیند ، قطعه به طور کامل درون فضای دو قالب قرار خواهد گرفت تا شکل مورد نظر بدست آید. در این روش یک قالب، نقش سندان و دیگری نقش چکش را دارد. قالب چکشی با وارد کردن ضربات متعدد موجب پرشدن حفرههای موجود در قالب دیگر میشود.
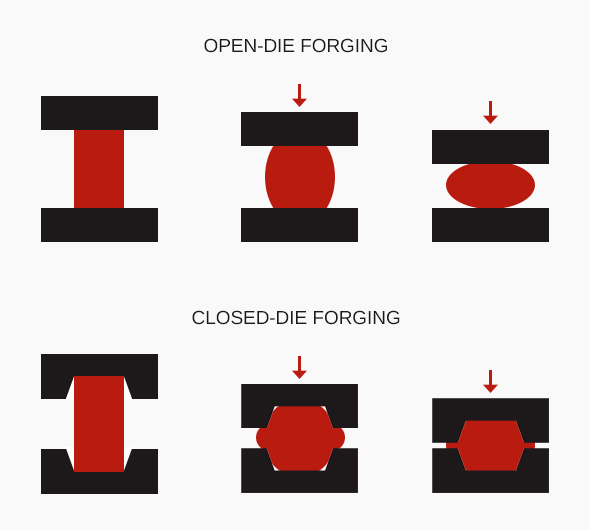
معایب و مزایای فورج فولاد
عملیات فورج اغلب به منظور ساخت قطعاتی با استحکام بالا و هندسههای متفاوت مورد استفاده قرار میگیرد. این فرآیند از شکل دهی فولاد در صنعت، یکی از روشهای نسبتاً کم هزینه و پرکاربرد می باشد. در آهنگری استحکام قطعه حاصل شده بیشتر می شود و نیز میتوان با انتخاب روش فورج مناسب، دقت ابعادی زیادی را بدست آورد. از مزایای فورج نیز میتوان موارد زیر را بیان کرد:
- افزایش خواص مکانیکی و خواص فیزیکی محصول تولید شده
- اتلاف و هدر رفتن کم مواد
- کاهش آلودگیها و ناخالصیهای ساختار فلز
اما در کنار مزایا، فورج فولاد معایبی نیز به همراه دارد و باید نسبت به آنها تا حدودی شناحت داشت. از معایب فورج فولاد میتوان موارد زیر را بیان کرد:
- به صرفه نبودن برای تولیدات اندک و جزئی
- هزینه زیاد تجهیزات و ابزار مورد نیاز
- محدودیت در تولید قطعات با هندسه و ابعاد پیچیده